Thermal Shock Resistant Fireproof Heat Insulating Brick
2018-03-14
Ceramic roller kiln is a new type of energy-saving kiln widely used in recent years with thousands of calcined building ceramics and also started to be used for calcining daily-use porcelain. Many of the building ceramics production areas in China have introduced such kilns. The refractory insulation bricks used in the kiln firing zone are the key furnace materials for the kiln. Because it is in direct contact with the flame, it should have good thermal shock resistance, high temperature volume stability, high temperature load conversion temperature, low thermal conductivity, and thermal insulation. Therefore, a new thermal shock insulation brick was produced.
Raw material composition and structure
Industrial alumina and Suzhou soil were selected as the main raw materials, and Tangshan Violet Festival and kyanite were added in small quantities. Increasing the amount of violetwood added will reduce the thermal shock stability. Industrial alumina is a white loose powder particles, composed of many γ-A1203 crystals with a size of 0.1 μm, an average particle size of 40-70 μm, a cubic structure, and irreversibly converted to a-Al203 at 1050-1500°C. There is a volume contraction.
The Suzhou soil is a white lightweight clay. The first mullitization was at 1300~1500°C, and the actual amount of production was only 90% of the theoretical production. The SiO2 and α-A1203 decomposed from Suzhou soil generate secondary mullite around 1300~1350°C, accompanied by volume expansion.
Kyanite contains 62.92% A1203 and 37.08% SiO2, and its chemical formula is Al203·Si02. During the heating process, it is irreversibly converted into a mixture of mullite and SiO2 with volume expansion and the conversion rate is about 79%. The conversion temperature of kyanite is from 1100 to 1410 °C.
From the above analysis, it can be seen that the volume shrinkage and the expansion caused by the phase change during the sintering process are basically offset, and the mullitization process can be completed at the established firing temperature. A certain amount of impurities in the raw materials will also promote the formation of mullite. Ingredients
The polystyrene spheres and clay were added first, and the alumina and kyanite powder were added after stirring. First stir for 3 minutes, then slowly add water to stir (the best amount of water is 28% to 30%). After the mud becomes a uniform plastic, bricks can be formed.
Forming
The use of steel molds for forming bricks with a plastic forming method reduces the forming moisture compared to casting molding and shortens the drying time. In addition, the size of the bricks that can be formed by the plastic method is easily controlled, thereby reducing the amount of plastic grinding of the products.
Fired
The use of downdraft kiln firing, firing temperature of 1400 ~ 1410 °C, heat 4 ~ 6 hours, to ensure that the products in the firing process melamine.
Machining
According to the user's needs, the fired products are cut and ground to produce standard, universal, exotic and special products.
The main crystal phase of the heat-resistant, shock-resistant and fire-resistant heat-insulating brick is mullite, which is mostly microscopic loose particles with amorphic amorphous structure. Between the pellets has been sintered with a small amount of columnar mullite grains. The secondary crystal phase is corundum and is columnar. The glass phase is dispersed in the grain boundaries and is less in number. Organizational structure: There is a thin dense layer on the surface of the crystal grains, and the grains have been sintered and bridged each other. The polystyrene ball burns and forms holes to form a porous structure with a porosity of more than 60%. Due to the low thermal conductivity of air, the brick has low thermal conductivity and excellent thermal insulation properties.
The melting point of the main crystal phase mullite is 1850°C, the melting point of the subcrystalline crystal corundum is 2050°C, and the mullite directly combines to form a strong network skeleton. This high melting point and strong structural skeleton enables the product to have volume stability, thermal shock resistance and high temperature strength at high temperatures. Practice has also proved that not only its working life can be comparable to imported products, but also the price has a clear advantage.
Based on domestic raw materials, the thermal shock-resistant fire-resistant insulation bricks produced by the application of the organic matter burning method and the plastic forming method have excellent seismic stability, heat insulation and high temperature structural strength. It is a new product with high quality and high efficiency and energy saving. Replace imported products. This product is completely suitable for the working conditions of ceramic roller kiln, but also can be used in ceramic kiln and other kilns.
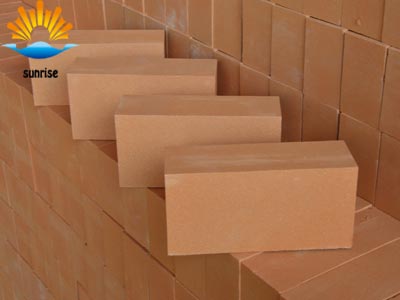