Cordierite-Mullite kiln furniture is the composition of Cordierite-Mullite and a glass phase. Due to the high temperature resistance of mullite and the low expansion of cordierite, Cordierite-Mullite kiln furniture get the good property of excellent thermal shock resistance. Cordierite-Mullite kiln furniture has the ability to work in long cycles safely at temperature below 1350℃,so it can fulfill the production demands of most ceramic.
1. Plain Batts
Plain Batts are the most common type of primary kiln furniture, usually produced by semi-dry pressing, but can also be made by pressure-casting. Extruded batts can be split into ten sub-categories as follows: Extra Large Batt, Extra Thin Batt, Plain Batt, Perforated Batt, Grooved Batt,Trapezoid Batt, Recessed Batt, Full Disc, Half Disc and Special Batt.
Extra Large Batt :Batts of various shapes over 3500cm2 in area.
Extra Thin Batt : Batts of all shapes under 9mm thick, excluding discs and half discs.
Plain Batt: Plain batts with an area ≤3500 cm2 and thickness≥9mm.
Perforated Batt : Batts with holes and an area ≤3500 cm2 and thickness≥9mm.
Grooved Batt: Batts with grooves and an area ≤3500 cm2 and thickness≥9mm.
Trapezoid Batt: Trapezoid batts with an area ≤3500 cm2 and thickness≥9mm.
Recessed Batt : Batts with an area ≤3500 cm2 and thickness≥9mm with locators.
Full Disc: Discs with and without centre holes.
Half Disc: Half discs with and without holes and cut-outs.
Special Batt : Any other plain batts not mentioned above.
Extruded batts have holes running the length of the cross section and are manufactured using high pressure vacuum extrusion, before being cut and surface-ground to guarantee the highest standard of flatness and dimensional accuracy. They are used mainly in the sanitaryware and glass panel industries, but can be found in a number of applications including the biscuit and glost firing of tableware.
Compared with plain batts, extruded batts have several advantages:
A. Weight reduction of approximately 35% - 50%, whilst increasing the load capacity of the batt. For example, a 38mm-thick extruded batt has the same weight as a 23mm-thick pressed batt of the same size, but can bear 5 times the load.
B. Energy Savings. Tests have shown that using extruded batts in a shuttle kiln firing glass panels, fuel consumption can be reduced by between 30% and 70%.
C. Reduced bend at high temperatures. 1200mm long extruded batts supported by silicon carbide beams have shown virtually no bend during use. This is extremely useful where flatness is critical, such as in the firing of glass panels.
D.Their ability to disperse heat is twice that of a solid batt of similar size, allowing them to bear extremes of hot and cold much better, thereby increasing their service life. This makes extruded batts especially suitable for faster firings.
Extruded batts can be split into eight sub-categories as follows: Thin Extruded Batt, Large Extruded Batt, Long Extruded Batt, Plain Extruded Batt, Perforated Extruded Batt, Cut-out Extruded Batt, Interlock Extruded Batt and Special Extruded Batt.
Thin Extruded Batt: Thickness under 25mm
Large Extruded Batt: Width over 590mm
Long Extruded Batt: Length over 1200mm
Plain Extruded Batt: Thickness ≥25mm, Width ≤590mm, Length ≤1200mm
Perforated Extruded Batt: Holes drilled into one or both faces of the batt
Cut-out Extruded Batt: Cut-out from the side of the batt to accommodate props, or large hole cut from the centre for use as a wash-basin / vanity-basin support.
Interlock Extruded Batt: Batts with a shiplap along one or both lengths to allow them to interlock in use.
Special Extruded Batt: Any extruded batt with special features not listed above.
Properties | Materials for ceramic kiln furniture | |||||||
L-Category | F-Category | R-Category | I-Category | C-Category | ||||
LUA | LEN | FON | FAC | ROY | LUK | COB | ||
Mineralogy | Cordierite- Mullite |
Cordierite- Mullite |
Cordierite- Mullite |
Cordierite- Mullite |
Cordierite- Mullite |
Cordierite- Mullite |
Cordierite- Mullite |
|
Chemical composition |
Al2O3 % | 40 | 41 | 36 | 39 | 41 | 43 | 46 |
SiO2 % | 49 | 48 | 52 | 49 | 47 | 46 | 44 | |
MgO % | 6.5 | 7.0 | 7.0 | 8.0 | 7.0 | 7.0 | 6.0 | |
Bulk density g/cm3 | 1.95 | 1.90 | 1.85 | 1.82 | 1.95 | 1.82 | 2.00 | |
Apparent porosity % | 26 | 28 | 28 | 29 | 26 | 33 | 25 | |
Expansion(20℃-1000℃/10-6K-1) | 2.3 | 2.3 | 2.6 | 2.2 | 2.2 | 2.5 | 3.1 | |
Thermal shock resisitance | ***** | ***** | ***** | ***** | ***** | ***** | ***** | |
Max working temperature | 1300 | 1250 | 1300 | 1320 | 1280 | 1280 | 1350 | |
Note:Data of properties listed above are the typical results from test pieces and therefore should be used only as guidance. |
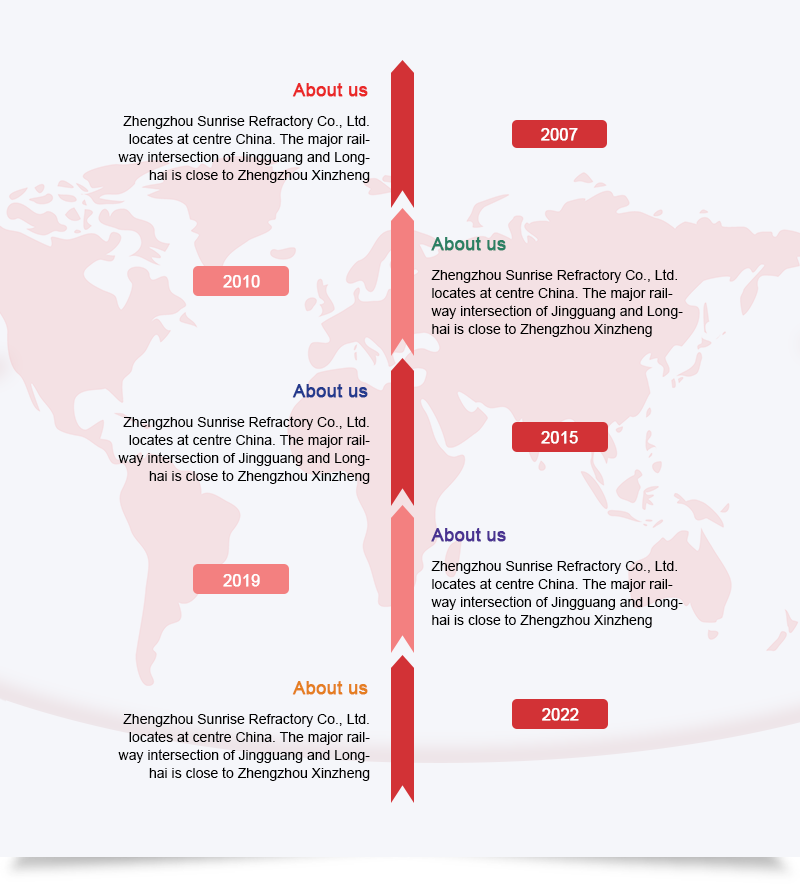
Factory strength »
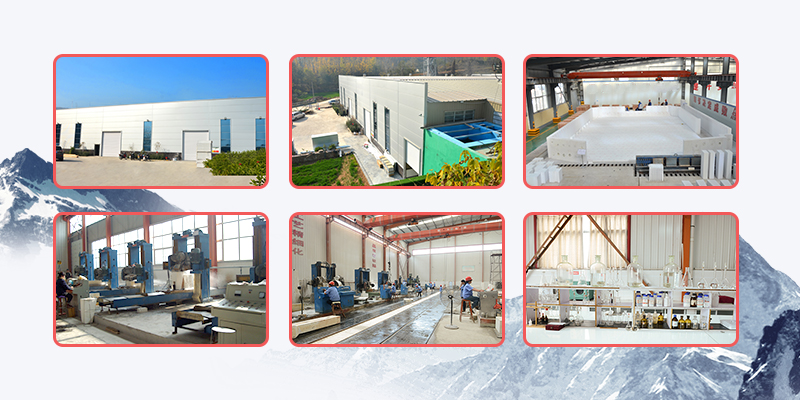
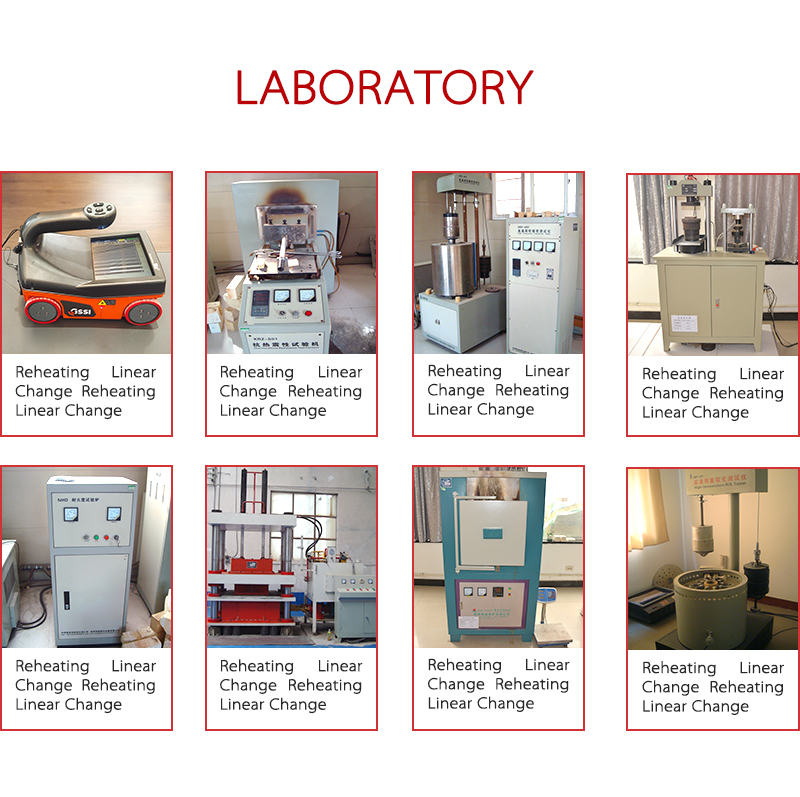