High alumina bricks have performance advantages
2018-05-21
In theory, aluminum silicate refractory materials with an Al2O3 content of more than 46% are called high-alumina bricks. China's provisions of high alumina brick Al2O3 content is greater than 48%. The higher the fineness of the natural high-alumina bauxite clinker + bonded clay fine powder, the more pronounced the promotion of sintering.
The proportion of high-alumina brick particles generally uses 3mm or 5mm critical particles, coarse particles 50-60%, medium particles 10-15%, fine powder 35-40%. Larger critical particles have advantages in improving thermal shock resistance and close packing of particles, but are prone to particle segregation, rough surface structure, and loose corners and edges. (Resistance to thermal shock - resistance to rapid changes in temperature and uneven heating capacity.) What are the sintering temperatures of high-alumina bricks: below 200 °C, elimination of residual moisture in the billet; 200-1250 °C, combined with kaolin in clay The stone dehydrates and decomposes to form mullite and free SiO2. Above 1250°C, α-Al2O3 in the clinker combines with free SiO2 to form secondary mullite, which accompanies volume expansion. (Note: The density of the generated phases is different.) We learned about the sintering temperature of high-alumina bricks. Then, what are the advantages of high-alumina bricks?
1, refractoriness. High-alumina brick products are high-grade products in aluminum silicate refractory products. Its refractoriness increases with the increase of Al2O3 content, generally not lower than 1750-1790°C. For corundum bricks with Al2O3 content greater than 95%, the refractoriness can be as high as 1900-2000°C.
2, load softening temperature. The load softening temperature of high alumina brick products decreases with the increase of silica and alkali metal oxide content, but is higher than that of clay brick products, and is about 1420-1530°C. Al2O3. The corundum brick with a content of more than 95% has a softening temperature of 1600°C or more.
3, slag resistance. Due to the neutrality and high content of Al2O3 in high-alumina brick products, these products have strong resistance to attack by acid-alkaline slag.
4, thermal shock stability. In high-alumina brick products, there are two crystals, corundum and mullite, coexisting, because the corundum has a larger thermal expansion coefficient than mullite. When the refractory brick temperature changes, the stress concentration is caused by the difference in expansion. Therefore, high alumina brick products have lower thermal shock stability than clay brick products, and the number of times of water cooling is only 3 to 5 times.
5, re-burn line changes. If the firing temperature of the high-alumina brick product is sufficient and the firing time is sufficient, the volume is stable, and the reburning line changes little; conversely, residual shrinkage such as a clay brick product occurs due to recrystallization.
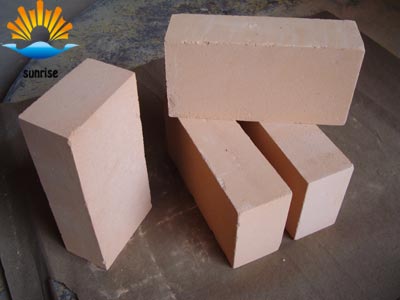